AB Astra LT presented its innovative Advanced Road Tanker at the Lithuanian Exhibition and Congress Centre LITEXPO on 27 May. The road tanker is made of stainless steel with exceptional features, designed for transporting liquid food products.
The AB Astra LT team, in cooperation with members of FTD LT (Food Technologies Digitalization LT) and BACC (Baltic Automotive Components Cluster) and other partners, having performed R&D in search of new solutions to the problem of safe road transport of liquid food products, has developed a new, lighter-weight and especially-well-insulated road tanker. During the event, potential partners from Lithuania and abroad were invited to see with their own eyes the new road tanker and the opportunities it offers to the food industry.
The event was organised in cooperation with the Agency for Science, Innovation and Technology (in Lithuanian, MITA). The opening speech was delivered by Dr Agnė Vaiciukevičiūtė, Deputy Minister of the Ministry of Transport and Communications of the Republic of Lithuania.
The event was moderated by the Chairman of the Board of BACC, Giedrius Valuckas, who expressed his firm support for the successful project. “On behalf of the FTD LT cluster and the Baltic Automotive Components Cluster, I would like to express our great pleasure with the presentation of this prototype of a truly exceptional product, the Advanced Road Tanker, designed to transport hot or refrigerated food products over long distances. The team of researchers and innovators at AB Astra LT has proven that we have enormous engineering potential right here in Lithuania, and we are able to create cutting-edge prototypes, manufacture them, and successfully bring them to market. Forecasts for international sales of the road tanker are bright, and we, the FTD LT and BACC clusters, will actively contribute to publicising and promoting sales of the new road tanker. The arrival of the new road tanker in the market will further strengthen AB Astra LT’s positions not only in Lithuania, but in export markets, too.”
An innovative product for the European market
From 2019 to 2021, AB Astra LT continuously worked on developing the new, especially-well-insulated road tanker, lighter than competing road tankers, for transporting liquid food products over long distances. The process of developing, producing and certifying the road tanker was completed last year, and this year pre-serial production is planned, to improve the manufacturing process. A little later, it is planned to start serial production.
According to Vaidas Liesionis, PhD, Chairman of the Board of the FTD LT cluster and General Manager of AB Astra LT, the road tanker is made of advanced Lean Duplex stainless steel. Until now, such stainless steel has not been used in the production of road tankers for transporting liquid food products, due to the complexity of working such stainless steel and especially due to the difficulty of welding such stainless steel. The AB Astra LT team overcame all these problems, creating and applying the necessary technologies for automated welding and post-welding processing, and the working of the advanced stainless steel no longer presents any difficulties.
Made of steel with exceptional properties
The new product features exceptional properties. The Duplex steel is perfectly suited for transporting or holding any liquid food products, including acidic (corrosive) food products or ingredients, for which austenitic steel cannot be used.
Such steel also has a yield strength (one of the most important mechanical properties of steel) twice as high as others, so the 3-section, 30m3-volume road tanker prototype is relatively light, weighing only 6,130 kg. Road tankers presently available on the market that are used to transport hot liquid products usually include a heating system, but this increases vehicle weight and reduces the cargo load capacity. In addition, the principle of using less insulation and compensating for the resulting heat loss by burning diesel in a heating system is not a sustainable solution. The same can be said for transporting refrigerated products, where it is essential to ensure that the temperature of such products does not increase beyond a certain limit.
The new road tanker is exceptionally well-insulated with a 110-mm-thick layer of next-generation monolithic polyurethane foam insulation, so its thermal conductivity is especially low, only 360W/m2K. The insulation level of the new road tanker produced by AB Astra LT is such that, after pouring into the road tanker 27 tonnes of chocolate at a temperature of +90 °C, the chocolate can be transported or simply stored for 11 days at an outdoor temperature of -20 °C without risk of the chocolate congealing, because after 11 days the chocolate will remain at a temperature of not less than +45 °C and can still be pumped.
In summertime, at an outdoor temperature of +20 °C, the same amount of hot chocolate (27 tonnes) requires 23 days to cool to a temperature of +45 °C. In addition, the excellent insulation properties allow the road tanker to be used not only as a vehicle for moving heated products, but also as a container for temporary storage at the client’s facility.
Getting ready for serial production
The factory is now preparing for serial production of the road tanker, and the new vehicle is already being used in test runs to transport liquid food products (oil, cream and so on).
The factory located in Alytus is one of the longest-operating metalworking companies in Lithuania. In addition, AB Astra LT today is one of the largest metalworking companies in Lithuania, designing and producing stainless-steel tanks and pressure vessels for use in the food, chemical and oil industries, well-known throughout the region as well as across Europe.
AB Astra LT exports its production to various countries. More than 85 per cent of its production is shipped to buyers in Finland, Sweden, Norway, France, Germany, Belgium, the Netherlands, the USA and other countries.
Attention to potential partners in Lithuania and abroad
During the event, Liesionis presented in detail the process of developing and producing the Advanced Road Tanker and highlighted the excellent results of the cooperation between AB Astra LT and researchers at the Lithuanian Energy Institute (LEI) and the Kaunas University of Technology (KTU).
Presentations were made by Andrius Vilkauskas, PhD, Dean of the Faculty of Mechanical Engineering and Design at KTU, and by Rimantas Levinskas, PhD, head of the Material Research and Testing Laboratory at
LEI.
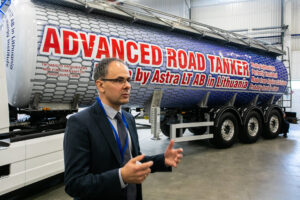
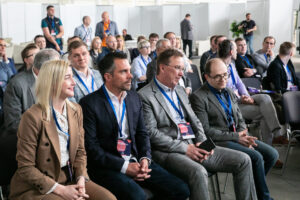
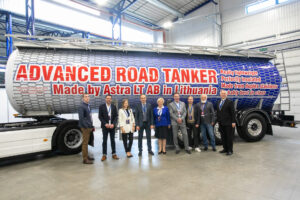
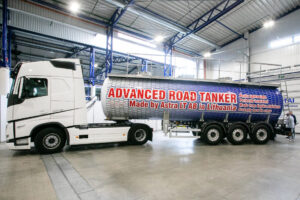